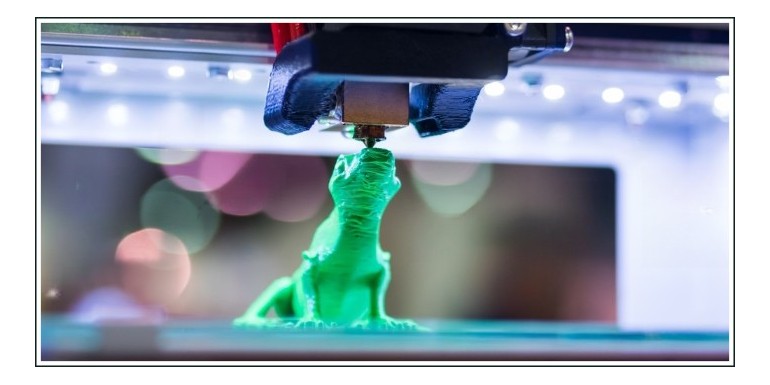
Fused Deposition Modeling (FDM) 3D printing is a widely used additive manufacturing technology that allows for the creation of complex three-dimensional objects. One of the key factors that significantly impacts the quality and success of FDM prints is the printing temperature. The temperature at which the filament is melted and extruded plays a vital role in achieving optimal layer bonding, adhesion to the build plate, and dimensional accuracy. In this article, we will explore the importance of optimizing printing temperature and provide insights into how to achieve perfect prints through temperature adjustment.
Understanding the relationship between Printing Temperature and Print Quality: The printing temperature directly affects the behavior of the thermoplastic filament during the printing process. Each filament material has its own ideal temperature range for extrusion, which is usually specified by the filament manufacturer. Deviating from this temperature range can result in various issues such as poor layer adhesion, weak interlayer bonding, or even complete print failure.
1. Experimentation and Material Properties:
Optimizing printing temperature often requires some experimentation to find the sweet spot for each specific filament. Factors such as the brand of filament, color, and even humidity can influence the ideal printing temperature. It is crucial to refer to the manufacturer's guidelines for a starting point and then fine-tune the temperature based on the desired print quality.
2. Effects of Temperature on Different Filament Types:
-
PLA (Polylactic Acid): PLA is one of the most popular filaments in FDM printing due to its ease of use and wide availability. The recommended printing temperature for PLA typically ranges from 190°C to 220°C. Higher temperatures may lead to stringing or oozing, while lower temperatures can result in poor layer adhesion.
-
ABS (Acrylonitrile Butadiene Styrene): ABS requires higher printing temperatures compared to PLA, usually ranging from 220°C to 250°C. It is essential to print ABS in an enclosed chamber to maintain a stable temperature and prevent warping. Higher temperatures help promote interlayer bonding, but excessive heat can cause layer splitting or delamination.
-
PETG (Polyethylene Terephthalate Glycol): PETG is known for its durability, flexibility, and transparency. It generally requires a printing temperature range of 220°C to 250°C. This filament has a narrower optimal temperature range compared to PLA, and deviations from the recommended range can lead to poor layer adhesion or brittleness.
-
TPU (Thermoplastic Polyurethane): TPU is a flexible filament that requires lower printing temperatures, typically ranging from 200°C to 230°C. Higher temperatures can cause over-extrusion and stringing, while lower temperatures can result in poor layer bonding and reduced flexibility.
3. Calibration and Bed Adhesion:
To optimize printing temperature, it is crucial to have a well-calibrated printer and ensure proper bed adhesion. Uneven bed leveling or incorrect nozzle height can impact the printing process and compromise print quality. Regular calibration and ensuring the correct distance between the nozzle and the bed are essential for achieving consistent results.
4. The Role of Slicing Software:
Slicing software, such as Cura, Simplify3D, or PrusaSlicer, provides control over various printing parameters, including temperature settings. These software tools allow users to adjust the printing temperature for different segments of the print, such as the initial layer, infill, or perimeters. By optimizing these temperature settings, users can achieve better print quality and address specific issues related to overhangs, bridging, or fine details.
5. Troubleshooting Common Issues:
Temperature optimization can help mitigate several common printing issues. For instance, warping can be reduced by increasing the printing temperature for the initial layers or by using a heated build chamber. Stringing and oozing can be minimized by lowering the temperature and adjusting retraction settings. By understanding the impact of temperature on these issues, users can troubleshoot effectively and achieve improved print results.
Conclusion:
Optimizing printing temperature is crucial for achieving high-quality prints in FDM 3D printing. By considering the specific characteristics of different filaments, conducting experimentation, and leveraging the control offered by slicing software, users can fine-tune their temperature settings to achieve flawless prints. Understanding the relationship between temperature and print quality, as well as addressing common issues through temperature adjustment, empowers users to overcome challenges and unlock the full potential of FDM 3D printing technology.